歯車は、動力の伝達や回転運動の変換を担う機械要素の一つであり、産業機械や自動車、航空機、精密機器など、あらゆる分野で欠かすことのできない存在です。高い精度と耐久性が求められる歯車は、単なる金属加工品ではなく、設計、加工、熱処理、仕上げ、検査に至るまで、全工程が一貫して管理されています。
一見するとシンプルに見える歯車も、その製造プロセスには高度な加工技術と専門的な知識が必要です。使用目的や性能要件に応じて、最適な材料選定や加工方法が選ばれ、各工程での品質管理も厳密に行われています。
本記事では、歯車加工の全体像を把握できるよう、工程ごとに具体的な内容を掘り下げて解説していきます。
歯車加工とは
歯車加工とは、機械内部で回転運動や動力を伝達する「歯車」を製造する一連の工程を指します。単に歯の形を彫るだけでなく、用途に応じた強度や精度を確保するために、素材の選定から始まり、切削・熱処理・研磨、そして最終検査に至るまで多段階のプロセスを経て仕上げられます。
特に歯車は回転体であることから、寸法誤差や歯面の精度がわずかでも機械全体の動作に大きく影響するため、他の部品以上に精密な製造管理が求められます。用途も多岐にわたり、軽負荷のプラスチック製から、重機・工作機械で使用される高硬度の鋼製まで種類も豊富です。
このように、歯車加工は単なる「部品の一つを作る工程」ではなく、要求される機能や環境に応じて最適化される、非常に高度な技術を要する分野といえます。
歯車加工の具体的工程
歯車が完成するまでには、設計・材料選定から始まり、切削や熱処理、仕上げ、そして最終検査に至るまで、いくつもの工程が段階的に進められます。
各ステップは独立しているように見えて、実際には次の工程の精度や加工性に大きく影響するため、全体として緻密な計画と管理が求められます。
ここでは、一般的な金属製の歯車を例に、代表的な加工フローを順を追って紹介していきます。
1.設計
まず最初に行うのが、使用用途に合わせた歯車の設計です。使用する機械の構造や荷重条件、回転数、耐久性などの要件に応じて、最適な歯形と寸法が決定されます。CADなどのツールを使って図面化します。
設計では、以下のような基本要素を定めます。
- モジュール(m):歯の大きさを表す単位で、歯車全体のサイズを左右します。
- 歯数:歯の本数。相手歯車との組み合わせにより減速比が決まります。
- 圧力角:歯と歯がかみ合う角度で、伝達効率や耐久性に影響します。
- 歯形:多くはインボリュート歯形が採用されますが、用途によってサイクロイド歯形やトロコイド歯形など異なる場合もあります。
- 歯幅、フェース幅:接触面の幅で、伝達できる力の大きさを左右します。
設計には専用のCADソフトや歯車設計ソフトが用いられ、図面や3Dモデルとして形にしていきます。また、必要に応じて有限要素解析(FEA)などを用いた強度シミュレーションを行い、トラブルの予測と対策を事前に検討します。
この段階でミスがあると、後工程すべてに影響を及ぼすため、正確かつ慎重な作業が求められる工程です。
2.材料調達
設計が完了したら、それに基づいて歯車の材料を選定・調達します。選ぶ材料によって、歯車の強度、耐摩耗性、加工性、さらにはコストや納期までもが大きく左右されるため、この工程は極めて重要です。
歯車の用途や動作条件に応じて、以下のような材料が用いられます。
- 炭素鋼(S45Cなど):汎用性が高く、機械構造用として広く用いられる。熱処理による強度向上も可能。
- 合金鋼(SCM415、SCM440など):焼き入れ性や耐摩耗性に優れ、高強度・高精度の歯車に多用される。
- 鋳鉄(FC、FCD):振動吸収性に優れ、静音性が求められる場面に適する。加工性も良好。
- 非鉄金属(アルミ、真鍮など):軽量で腐食に強く、小型機器や試作向けに用いられる。
- 樹脂(POM、ナイロンなど):静音性が高く、潤滑不要な用途に。低負荷の機構に適している。
3.旋盤加工(切削、形状加工)
材料が準備できたら、旋盤加工を行います。これは素材を円筒形に成形し、歯切り加工のための土台を整える工程です。高精度な歯車を製作するには、基準となる外径や中心穴(ボア)の加工精度が極めて重要となります。
旋盤加工では、以下のような作業が行われます。
- 外径の仕上げ:材料の表面を切削して円筒形に整える。歯形の基準面にもなる重要な寸法。
- 中心穴(ボア)の加工:軸に取り付けるための内径を加工。嵌合(はめあい)の精度が重要。
- 端面の直角出し:歯車の平面部を加工し、回転軸との直角精度を確保。
- キー溝の下穴加工:後工程でキー溝加工を施すための準備。
NC旋盤(数値制御旋盤)を用いることで、高い寸法精度と加工効率が両立され、複雑な形状や多工程の自動化も可能になります。なお、この段階で発生する加工誤差や同心度のズレは、歯切りや歯研の精度にも直接影響するため、極力避ける必要があります。
旋盤加工は、歯車製作における“下地づくり”の工程であり、この精度が仕上がり全体の品質を左右すると言っても過言ではありません。
4.歯切り加工
旋盤加工によって基本形状が整った素材に対し、歯車としての最も重要な特徴である「歯」を形成していくのが、歯切り加工の工程です。
この加工には専用の機械が使われ、歯の形状やサイズ、かみ合い精度が設計通りに再現されるよう、非常に高い精度で進められます。歯切り加工は大きく分けて、素材を荒く削る「粗加工」と、精密な仕上がりを目指す「仕上げ加工」の2段階で行われます。
4-1.粗加工(ホブ盤などによる歯切り)
粗加工では、主に「ホブ盤」が使用されます。これは「ホブ」と呼ばれる円筒状の刃物を回転させながらワーク(加工物)に当てていく方式で、連続的に歯形を削り出すことができます。
この方法は切削速度が速く、同じ形状の歯車を大量に生産するのに適しているため、量産工程の中心を担っています。また、ウォームホイールやギヤシェーパーなど、歯形や仕様によっては他の専用機械が使われることもあります。
ホブ切りの時点では若干のバリや粗さが残るため、この後の仕上げ工程で精度をさらに高める必要があります。
4-2.仕上げ加工(シェービング、ブローチなど)
粗加工で形成された歯面を、より滑らかに、かつ正確な形状へと整えるのが仕上げ加工です。歯車の用途によっては、この工程を省略することもありますが、高精度な駆動が求められる場面では欠かせません。
代表的な仕上げ加工としては「シェービング加工」があり、専用のシェービングカッターを用いて歯面を微細に削ります。これにより、表面粗さの改善とともに、ピッチ誤差やかみ合い率の向上が期待できます。
また、インターナルギアや特殊形状には「ブローチ加工」が用いられることもあります。これは一度に多数の刃を通すことで、短時間で高精度な加工が可能となる方法です。
5.面取り
歯切り加工が完了した後、歯の先端や端面などにできた鋭角部を削り取り、滑らかに整える工程が「面取り(バリ取り)」です。加工後の歯車には微細なバリや角が残っていることが多く、これを放置すると、組み立て時の損傷やけが、さらには他部品との干渉による不具合の原因となる場合があります。
面取りは、歯の先端や側面のエッジを45度程度の角度でわずかに削ることで、過度な鋭利さを取り除く作業です。面取りの大きさや形状は、図面で指示されることが一般的です。主に以下のような目的で行われます。
- 作業者の安全確保:鋭利なエッジによるけがを防ぐ
- 組立性の向上:歯車同士や軸とのスムーズな嵌合を実現
- 疲労やクラックの防止:応力が集中しやすい角を丸めることで、疲労破壊のリスクを低減
面取り加工には手作業のバリ取り工具や、エッジカッター、さらにはNC機による自動面取り機構が使われる場合もあります。シンプルな作業に見えて、製品の品質と信頼性を左右する、品質を左右する重要な工程の一つです。
6.熱処理、焼き入れ
歯切り加工や面取りが完了した歯車に対し、さらに強度や耐摩耗性を高めるために行うのが「熱処理」です。特に歯面に高い負荷がかかるような用途では、焼き入れなどの熱処理を施すことで、寿命と信頼性を大幅に向上させることができます。
熱処理とは、金属を加熱・冷却することでその性質を変化させる工程で、歯車においては主に以下のような処理が行われます。
- 焼き入れ(表面硬化):鋼材を高温に加熱し、急冷することで表面を硬化。耐摩耗性を大きく向上させる。
- 焼き戻し:焼き入れ後に適度な温度で再加熱し、内部応力を除去して靭性(粘り強さ)を付与。
- 浸炭焼き入れ:低炭素鋼の表面に炭素を浸透させてから焼き入れを行い、硬化層を形成。重荷重用途に多い。
- 高周波焼き入れ:誘導加熱により表面のみを短時間で加熱・冷却。寸法変化を抑えながら高硬度を得られる。
熱処理は素材の種類や歯車の形状、要求性能に応じて最適な方法を選定する必要があります。処理後は若干の変形が生じることもあるため、後工程での研削や歯研などによる精度補正も見越した設計・加工計画が重要です。
適切な熱処理を行うことで、歯車は高トルク・高回転の過酷な環境でも安定して機能するようになります。
7.研磨、研削、歯研
熱処理を終えた歯車は、表面硬度が増して高い耐久性を持つようになりますが、その一方で、熱によるわずかな歪みや寸法の狂いが発生することもあります。こうした微細な誤差を補正し、歯形や歯面をさらに高精度に仕上げるのが「研磨」「研削」「歯研(はけん)」の工程です。
この工程は、歯車の回転精度やかみ合いの滑らかさ、騒音低減などに直結するため、特に高精度を要求される歯車には欠かせません。
- 研磨(一般的な表面研磨):歯車の外径や端面などを平滑にする加工。焼き入れ後の変形補正にも用いられます。
- 研削:砥石を用いて材料を高精度で削る方法。焼き入れ後の硬化層でも加工が可能です研削加工には、円筒研削、平面研削、内面研削など、様々な種類があります。。
- 歯研(歯面研削):専用の歯車研削盤を用いて、歯のかみ合い面そのものをミクロン単位で調整する加工。最も高精度な仕上げ方法の一つです。
歯研は、歯面の形状誤差やピッチ誤差を補正することで、伝達効率や静粛性を大幅に向上させます。特に、工作機械、ロボット減速機、航空・自動車用の高性能ギアなど、精密かつ高負荷の用途ではこの工程が不可欠です。
また、仕上げ加工の精度を保つためには、砥石の選定や研削条件の設定、加工中の温度変化管理などにも高度な技術が求められます。歯車の最終的な性能は、この工程の仕上がりに大きく左右されると言えるでしょう。
8.検査
すべての加工工程を経た歯車は、最後に「検査」を行い、設計通りの寸法・精度・性能が確保されているかを確認します。歯車は回転運動の中核を担う部品であるため、ごくわずかな誤差でも振動や騒音、寿命低下の原因となることがあります。そのため、出荷前の検査は非常に重要です。
検査では主に以下のような項目が評価されます。
- 歯形誤差:理想的な歯形とのずれを評価
- ピッチ誤差:歯と歯の間隔が均一かどうかを確認
- 歯筋誤差:歯の幅方向に沿った歯形の直線性
- バックラッシ:かみ合い時の歯と歯のすき間
- 全体振れ・同心度:軸とのズレや回転バランスの確認
これらの検査には、専用の歯車測定機や三次元測定機、ダイヤルゲージ、ピンゲージなどの測定器が用いられます。高精度な歯車では、測定単位もミクロン(1/1000mm)レベルとなり、環境温度や測定者のスキルによっても影響を受けるため、恒温室内での測定や自動測定装置の導入が進んでいます。
検査結果は、出荷時の検査成績書や品質保証書として顧客に提供されることも多く、トレーサビリティの確保や後工程での安心につながります。加工技術と同じく、正確な検査体制が信頼される歯車製作には欠かせない要素です。
歯車加工に使用される機械
精密な歯車を製作するには、各工程に最適化された専用の工作機械が不可欠です。設計通りの形状と精度を実現するためには、高度な制御性能と剛性を備えた機械設備が必要とされ、用途や加工内容に応じて多種多様な装置が使い分けられます。近年では、数値制御(NC)技術の導入により、加工精度と生産性が飛躍的に向上しています。
ここでは、歯車加工で主に使用される代表的な機械について、その特徴や用途を交えて紹介します。
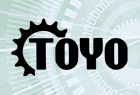
歯切り盤
歯切り盤は、「歯車の歯」を切削するための専用工作機械で、歯車加工の中心的な存在です。用途や歯車の形状に応じてさまざまな種類があり、精度や生産性を左右する重要な装置として位置づけられています。
主に使用される歯切り盤には以下のようなタイプがあります。
- ホブ盤(ホブマシン):円筒状のホブカッターを用いて、素材と刃物を回転させながら連続的に歯を形成する方式です。直歯・はすば歯などの外歯車の量産に最も広く用いられています。スカイビング法により内歯車の歯切りに対応できる機種もあります。
- NCホブ盤:数値制御機能を搭載したホブ盤です。高精度な繰り返し加工や、複雑な歯形補正、多軸制御による高効率加工が可能です。自動工具交換(ATC)機能を持つ機種もあります。
- ギヤシェーパー:シャンク状の刃物を上下に往復運動させて歯を切削する方式です。内歯車や段付き歯車など、ホブ盤では加工困難な形状にも対応可能です。創成形歯切りと成形歯切り両方に対応できる機種があり、ピニオンカッタを用いた歯切りもこの一種です。
- NCギヤシェーパー:数値制御により、複雑な歯形や動作を高精度に実現します。
- その他の歯切り盤:ベベルギヤ(かさ歯車)専用の歯切り盤や、ウォームギヤ専用の創成盤など、特殊な歯形に対応した機械も存在します。これらの機械にもNC制御が導入され、高精度化が進んでいます。
歯切り盤の選定は、加工する歯車の種類・寸法・精度要求によって決定されます。たとえば、大径ギヤや高精度ギヤには剛性の高い大型機が必要となり、小型精密歯車では細かな送りや補正機能が重視されます。
歯車研削盤
歯車研削盤は、熱処理後の硬化した歯車の歯面を、砥石を用いて精密に仕上げるための工作機械です。歯面の形状誤差やピッチ誤差をミクロン単位で修正し、伝達効率や静粛性を大幅に向上させます。
- NC歯車研削盤:数値制御により、砥石の動作や送り量を精密に制御し、高精度な歯面研削を実現します。複雑な歯形補正や、クラウニング、エンドリリーフなどの特殊な形状の創成も可能です。プロファイル研削盤、創成研削盤など、様々な方式があります。
その他の機械
歯車加工には、歯切り盤や歯車研削盤以外にも、多くの補助的な工作機械や装置が関わっています。それぞれの工程に適した機械を使い分けることで、安定した加工精度と作業効率を実現することが可能です。
以下に、歯車加工で広く使用される主な機械を紹介します。
- 旋盤:素材の外径や中心穴、端面を加工する基本的な機械で、歯切り前のブランク加工に使用されます。NC旋盤は、複雑な形状を高精度かつ効率的に加工できます。
- フライス盤:平面や溝、キー溝などの切削加工を行う機械で、歯車に取り付けるためのキー溝加工などで使用されます。NCフライス盤やマシニングセンタは、複雑な形状のキー溝やスプライン加工にも対応できます。
- ブローチ盤:複数の刃を持つブローチ工具を一方向に通して加工する方式。特に内歯車やキー溝の高精度仕上げに使用されます。
- 研削盤(歯車研削盤を除く):外径研削盤や平面研削盤など、熱処理後の硬化素材に対して、歯面以外の部分を高精度で表面を整える加工を行います。NC研削盤は、高い寸法精度と面粗さを実現します。
- 熱処理装置:高周波焼き入れ装置や浸炭炉など、歯車の強度や耐摩耗性を向上させるための専用装置です。
- 歯車測定機:加工後の歯車の寸法や精度を測定する専用の機械です。NC制御により、自動で多項目を高精度に測定できる機種が主流となっています。
これらの機械は、各工程を支える存在として欠かせないものです。ひとつの歯車が完成するまでには、これら複数の設備が連携し、正確かつ効率的に加工が進められていきます。生産体制や加工精度を左右するため、設備の整備状況も品質確保の重要な要素となります。
歯車加工の精度管理
歯車は回転運動や動力を正確に伝える部品であるため、加工精度が製品の性能や耐久性に直結します。そのため、製造現場では寸法精度やかみ合い精度を維持するための「精度管理」が極めて重要な役割を果たします。
わずかな形状誤差や組み立て精度の乱れが、振動、騒音、摩耗といった不具合を引き起こす原因となるため、各工程での精密な加工とあわせて、検査・測定・記録の体制が整えられています。
ここでは、歯車加工における主な検査方法や、近年の技術進歩による精度管理の高度化について紹介します。
検査方法
歯車の品質を確保するためには、加工後に各種の精度項目を測定し、図面通りに仕上がっているかを確認する必要があります。これらの検査は、完成品としての性能や信頼性を保証する上で欠かせない工程です。
歯車の検査でよく用いられる測定項目と代表的な方法は、以下の通りです。
- ピッチ誤差:隣接する歯の間隔のばらつきを測定。専用のピッチ測定機や歯車検査機を使用。
- 歯形誤差:理想的なインボリュート曲線とのずれを評価。歯形試験機で測定し、正確なかみ合い形状を確認。
- 歯筋誤差:歯の幅方向に沿った歯形の直線性を評価。偏摩耗やかみ合い不良の予兆にもつながる。
- バックラッシ:かみ合い時のすき間(遊び)の測定。相手歯車との組み合わせで確認。
- 振れ・偏心:回転軸に対する歯車の中心位置のズレを確認。ダイヤルゲージや三次元測定機で評価。
これらの測定には、専用の歯車測定機(ギアメジャー)や三次元測定機、マスターギヤとのかみ合い検査装置などが使用されます。高精度な歯車では、ミクロン単位での誤差が許容値となることも珍しくありません。
まとめ
歯車加工は、設計・材料選定から始まり、切削、熱処理、仕上げ、検査に至るまで、多くの工程と高度な技術が求められる精密な製造プロセスです。一見単純に見える部品であっても、その内部には微細な調整と積み重ねられた職人技、そして最先端の加工技術が凝縮されています。
各工程が密接に関係しており、ひとつでも精度を欠けば、全体の性能や信頼性に直結してしまいます。だからこそ、各段階での的確な判断と品質管理が極めて重要です。
この記事を通じて、歯車がどのように作られ、どのような機械と工程で高精度な部品として仕上がっていくのか、その全体像が少しでも明確になれば幸いです。