歯車の性能を最大限に引き出すためには、使用環境や求められる機能に適した材料を選ぶことが非常に重要になります。
本記事では、歯車によく用いられる代表的な材料の種類から、それぞれの特徴、そしてどのような場面でその特性が活かされているのか、さらには材料ごとの一般的な加工方法についても解説します。
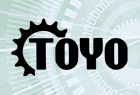
金属材料
金属材料は、歯車の製造において最も広く使用されている素材群です。その理由は、優れた機械的特性(高い強度・剛性・耐摩耗性)を持ち、加工技術や熱処理技術が確立されているためです。特に、負荷の大きい機械や高精度が要求される機構部品においては、金属歯車が不可欠となります。
歯車に求められる主な性能には、以下のようなものがあります。
- トルクの伝達能力(高強度)
- 耐摩耗性・耐疲労性(長寿命)
- 寸法精度(正確なかみ合い)
- 熱安定性(高温環境での性能保持)
金属材料はこれらの性能に対応しやすく、かつ材質や熱処理方法の選択によって、強度と靭性、耐久性と加工性のバランスを取ることが可能です。また、加工法においても、切削・歯切り・研削・焼入れなどの各工程が精緻に確立されており、量産と高精度の両立が可能になっています。
金属材料には、炭素鋼、合金鋼、ステンレス鋼、鋳鉄などの種類があります。これらはそれぞれ、コスト、強度、耐腐食性、加工性、騒音特性、振動吸収性などの面で異なる特性を持っており、使用目的や動作環境に応じて使い分けられています。
以下では、代表的な金属材料ごとに特徴・メリット・デメリット・採用例を詳しく紹介します。
炭素鋼(S45Cなど)
炭素鋼は、鉄に炭素を含有した最も基本的な鋼材であり、特に中炭素鋼(S45Cなど)は歯車材料として広く使われています。炭素含有量が約0.4~0.5%程度のものは、機械的強度と加工性のバランスが良く、コストも比較的安価なため、汎用的な用途で多く採用されています。
また、熱処理(焼入れ・焼戻し)によって、表面硬度を高めることができ、耐摩耗性を改善することも可能です。さらに、炭素鋼は切削性も良好で、旋盤・フライス・ホブ盤など、一般的な機械加工に適しています。
メリット
- 切削加工や歯切り加工が比較的容易で、汎用的な材料であるため入手しやすい
- 熱処理で強度・硬度の調整がしやすい
- コストパフォーマンスに優れる
デメリット
- 耐食性が低く、錆びやすい
- 高温環境下では軟化しやすく、高負荷が連続する条件下では疲労強度や耐摩耗性が合金鋼に劣る
主な用途
自動車のエンジン周辺部品(補助的なギアなど)、産業用機械の減速機、農業機械の駆動部、コンベヤなどの一般的な動力伝達用ギアなどに用いられます。特に、コストと性能のバランスが重視され、過酷すぎない環境で中程度の強度・寿命が求められる箇所に最適です。
合金鋼 (SCM415、SNCMなど)
合金鋼は、鉄に加えてクロム、ニッケル、モリブデンなどの合金元素を加えた鋼材で、炭素鋼に比べてより高度な機械的特性を持ちます。中でもSCM(クロムモリブデン鋼)やSNCM(ニッケルクロムモリブデン鋼)は、焼入性が高く、耐摩耗性・疲労強度・靭性が優れているため、高負荷環境に適しています。
特に浸炭焼入れ処理との相性がよく、表面は非常に硬く、芯部は靭性を持った「肌焼鋼」として、自動車のトランスミッションギアやギアボックスなどの重要部品に多く使用されます。歯車の精度や寿命を大幅に向上させることができ、高い回転数や衝撃荷重にも耐える性能を発揮します。
メリット
- 優れた表面硬度と耐摩耗性
- 靭性や疲労強度も高く、割れにくい
- 精密な切削加工や歯切り加工が可能であり、熱処理後の歪みが少ないため、高精度な研削仕上げにも適している
デメリット
- 炭素鋼に比べて被削性が低く、特に焼入れ後や浸炭焼入れ後の硬い状態では切削が困難になる
- 材料費・処理費が高くなる傾向がある
主な用途
自動車のトランスミッションギア、エンジン部品(クランクシャフトギアなど)、建設機械の駆動ギア、航空機のランディングギアやエンジン部品、産業用減速機の高速回転ギアなど、高負荷・高回転かつ高い信頼性が求められる重要な歯車に広く用いられます。
ステンレス鋼(SUS304、SUS630など)
ステンレス鋼は、質量比で10.5%以上のクロムを主成分とし、表面に不動態皮膜を形成することで、優れた耐食性・耐酸化性を発揮する鋼材です。錆びにくく、水分や薬品などが存在する腐食性の高い環境下でも長期間安定した性能を保ちます。代表的なSUS304などのオーステナイト系ステンレス鋼は、非磁性であり、比較的加工性に優れているため、衛生性が求められる食品機械や医療機器などに適しています。
また、SUS630(析出硬化系ステンレス鋼)のように、時効硬化処理などの熱処理によって非常に高い硬度・強度を得られる種類もあり、高い耐摩耗性が要求される用途にも有効です。ただし、オーステナイト系を含め、一般的に炭素鋼や合金鋼よりも切削性が劣るため、低速切削や高剛性の工作機械、適切な工具の選定が重要になります。
メリット
- 優れた耐食性(錆びにくい)
- 熱処理可能な種類では高強度も得られる
- クリーン環境での使用に適する(食品・医療)
デメリット
- 加工が難しく、工具摩耗が激しい
- 一般的にコストが高い
主な用途
食品製造装置、医療機器、化学プラント、水中装置、海洋機器など。衛生性や耐腐食性が最優先される環境下での歯車に使用されます。
鋳鉄(FC材、FCD材)
鋳鉄は、一般的に炭素を2%以上含む鉄合金で、溶融した金属を鋳型に流し込んで成形する「鋳造」によって、複雑な形状の部品を比較的容易に製造できることが大きな特徴です。FC材(ねずみ鋳鉄)は、黒鉛の片状組織により振動吸収性や潤滑性に優れ、比較的安価であるため、工作機械のベッドやハウジング、大型ギアボックスなどに利用されます。
一方、FCD材(ダクタイル鋳鉄)は、球状黒鉛を含んだ構造で、靭性や引張強さが大きく向上しており、より高負荷の用途にも対応可能です。鋳造後には切削加工で仕上げる必要がありますが、全体的なコストパフォーマンスに優れる素材と言えます。
メリット
- 振動吸収性が高く、運転音の低減に貢献
- 鋳造で複雑形状が製造できる
- 潤滑性がよく、摩耗が少ない
デメリット
- 一般的に、鍛造された鋼材と比較して、引張強度や衝撃靭性などの機械的強度は低い傾向がある
- 薄肉・高精度品には不向き
主な用途
工作機械の主軸やベッド、大型の産業機械用歯車装置、低速回転の減速機、農業機械のフレームやハウジングなど、振動吸収性や剛性が求められる比較的大きな構造部品や、自己潤滑性が有効な箇所に利用されます。
非金属材料
非金属材料は、近年さまざまな産業分野で需要が高まっている歯車材料です。主に高分子樹脂(エンジニアリングプラスチック)が使われ、軽量、自己潤滑性、低騒音、耐薬品性、電気絶縁性といった金属にはない特性を持っています。
特に、軽負荷・中負荷で動作する機構、給油が困難な箇所、静音性が要求される用途において、樹脂歯車は有効な選択肢となります。材料自体が持つ自己潤滑性により、グリースやオイルなどの潤滑剤を使用できない機構でも、比較的長期間にわたり安定した動作が期待できます。また、加工方法としては射出成形による大量生産が可能なため、家電やOA機器などの量産品にも広く使われています。
ただし、樹脂歯車にはいくつかの制約も存在します。耐熱性や強度、寸法安定性、吸湿による影響などに注意する必要があります。たとえばポリアミドは吸水性が高く、湿度変化により膨張してかみ合い精度に影響を及ぼすことがあります。これらの材料特性を正しく理解し、設計・用途に応じた適切な材質選定が不可欠です。
非金属材料の中でも、代表的なものとして、機械的特性と自己潤滑性に優れるポリアセタール(POM)、強度と耐摩耗性に優れるポリアミド(PA)、透明性と耐衝撃性に優れるポリカーボネート(PC)、そして、より高い耐熱性や耐薬品性、強度を持つポリフェニレンサルファイド(PPS)やポリエーテルエーテルケトン(PEEK)などがあり、それぞれに固有の特性を有しています。
以下では、非金属材料ごとにその特性とメリット・デメリット、使用例を詳しく見ていきましょう。
ポリアセタール(POM)
ポリアセタール(Polyoxymethylene、POM)は、エンジニアリングプラスチックの中でも代表的な材料で、高い機械的強度・耐摩耗性・寸法安定性を備えています。特に「自己潤滑性」に優れており、歯車同士が潤滑剤なしでもスムーズに動作できるのが大きな利点です。
POMは耐薬品性にも優れ、多くの中性・アルカリ性の薬品に対して安定しており、環境的に厳しい箇所にも対応できます。また、熱変形しにくく、高精度な歯車の寸法保持がしやすいことから、精密機器に多用されています。
メリット
- 自己潤滑性が高く、給油不要の設計が可能
- 寸法精度に優れ、長期使用でも狂いが少ない
- 耐摩耗性・耐薬品性が高く、耐久性がある
- 成形加工が容易で量産に適している
デメリット
- 連続使用における耐熱性は比較的低く、一般的に約100~120℃程度が上限となる
- 耐紫外線性に乏しく、屋外での長期使用には注意が必要
- 強い酸には弱い
主な用途
プリンター、コピー機、FAXなどのOA機器、窓やドアの開閉機構などの住宅設備、自動車のワイパー機構やパワーウィンドウ部品などの内装部品、小型家電の駆動機構など、小型で中軽負荷の歯車、給油が困難な箇所、静音性が求められる用途に広く採用されています。
ポリアミド(PA、ナイロン)
ポリアミド(Polyamide、PA)は、一般的にナイロンの名称で広く知られる合成樹脂であり、柔軟性、優れた耐摩耗性、および高い耐衝撃性を有する素材です。特に耐摩耗性はポリアセタール(POM)に匹敵するレベルであり、繰り返し摺動や衝撃のかかる用途に適しています。
ポリアミドは高い弾性を有しており、歯車のかみ合い時に発生する衝撃を緩和し、騒音を低減する効果があります。また、ある程度の自己潤滑性も示すため、軽負荷条件下では無給油での使用も可能です。
一方で、吸水性が高いという特性を持つため、高湿度環境下では吸水による膨張が生じ、寸法精度が要求される用途においては設計段階での考慮が不可欠です。
メリット
- 耐摩耗性、耐衝撃性に優れる
- ある程度の自己潤滑性を示し、弾性と相まって静音性に貢献する
- 弾性があり、ギア噛み合い時の衝撃を和らげる
- 成形加工がしやすく、複雑形状にも対応
デメリット
- 吸水性が高く、湿度環境による寸法変化がある
- 長期間の高温環境下では劣化しやすい
- 耐紫外線性が低く、屋外用途には不向き
主な用途
自動車部品(ドアロック機構、ワイパーギア、シートベルト機構など)、繊維機械、食品包装機械、家電製品の駆動部品など、中程度の負荷で静音性や耐衝撃性が求められる用途、およびある程度の自己潤滑性が有効な箇所に用いられます。
ポリカーボネート(PC)
ポリカーボネート(Polycarbonate、PC)は、高い透明性、優れた耐衝撃性、および比較的高い耐熱性を有するエンジニアリングプラスチックです。特にその耐衝撃性は非常に高く、同形状のポリアセタール(POM)やポリアミド(PA)と比較しても優れた値を示します。その透明性を活かし、内部の可視化や光透過性が求められる用途、例えば透明なギアが必要な場面などで利用されます。
また、比較的高い耐熱性を持ち、連続使用温度として約120~130℃程度まで安定した使用が可能です。しかしながら、耐摩耗性は他のエンジニアリングプラスチックと比較してやや劣るため、使用条件によっては適切な潤滑が必要となる場合があります。加えて、一部の有機溶剤や強アルカリに対する耐性は限定的です。
メリット
- 優れた透明性と光学的特性
- 極めて高い耐衝撃性(壊れにくい)
- 耐熱性が高く、成形変形も少ない
- 静電気対策や難燃性を持たせる改良も可能
デメリット
- 耐摩耗性が比較的低いため、高負荷や連続摺動条件下では摩耗が進行しやすく、歯車としての寿命が制限される可能性がある
- 化学薬品に対して脆弱な場合がある(特にアルカリ)
- 吸湿性もあるため、使用環境に注意
主な用途
カメラやプロジェクターなどの光学機器、血液分析器などの医療機器、玩具の駆動部、家電製品の筐体や内部機構など、透明性や高い耐衝撃性が求められる用途、および比較的高い耐熱性や難燃性が要求される環境で使用されます。
その他の樹脂(PPS、PEEKなど)
ポリフェニレンサルファイド(PPS)やポリエーテルエーテルケトン(PEEK)は、高温・高負荷環境でも安定して使用できる高機能エンジニアリングプラスチックです。耐熱性・耐薬品性・寸法安定性に極めて優れ、過酷な条件下でも性能を維持できるため、航空宇宙や医療分野でも使用されます。
ポリフェニレンサルファイド(PPS)は自己消火性を有する難燃性材料であり、連続使用温度は約200℃程度です。一方、ポリエーテルエーテルケトン(PEEK)は、さらに高い連続使用温度(約260℃)に耐えることができ、樹脂材料の中でも最高レベルの機械的強度を示します。ただし、どちらも非常に高価で、加工にも専門的な技術が必要です。
メリット
- 非常に高い耐熱性・耐薬品性
- 寸法安定性が高く、高精度なギアに適する
- 長期的な耐久性に優れ、特殊環境での使用が可能
デメリット
- 材料費が高価で、コスト面での制約がある
- 成形や切削加工には高度な技術が必要
- 大量生産には適さず、用途が限られる
主な用途
航空宇宙産業のエンジン部品、高度な医療機器の駆動機構、半導体製造装置の精密部品、腐食性流体を扱う化学プラントのポンプ部品など、高温、腐食性薬品、および高い寸法精度が同時に要求される特殊な環境下で使用される歯車や機構部品に採用されます。
材料選定のポイント
歯車の材料選定は、設計段階で最も重要な判断の一つです。機械の信頼性・寿命・性能・コストに大きく関わるため、使用条件に適した材料を慎重に選定する必要があります。以下に代表的な判断要素と、それぞれにおける具体的な考慮点を解説します。
負荷の大きさ(トルクや衝撃)
歯車が受けるトルク(ねじり力)や衝撃の強さは、材料選定において基本となる指標です。
たとえば、重機や建設機械の駆動部では、断続的または連続的に高い負荷が加わるため、靭性や疲労強度に優れた合金鋼(SCM415、SNCMなど)が適しています。一方で、OA機器や家電製品など負荷の小さい用途では、ポリアセタール(POM)やポリアミド(PA)などの樹脂材料が十分な性能を発揮します。
- 高負荷・衝撃大 → 合金鋼(高い引張強度、靭性、疲労強度、焼入れによる高硬度化)
- 中負荷・中程度の衝撃 → 炭素鋼(適切な強度、良好な加工性、熱処理による強度向上、コストバランス)
- 低負荷・衝撃小 → 樹脂材料(自己潤滑性、軽量性、低騒音性、耐薬品性、コストメリット、設計自由度)
回転速度(スピード)
歯車が高速回転するかどうかも重要な要素です。高速で回転する場合、摩擦や発熱が大きくなり、摩耗や変形、騒音の発生が懸念されます。
- 高速回転 → ポリアセタール(POM)のような軽量で自己潤滑性が高い樹脂が適する場合があります。また、精密加工された合金鋼製歯車(表面仕上げ良好)も有効です。
- 低速回転 → 摩耗や騒音の影響が少なくなるため、鋳鉄や炭素鋼なども採用しやすくなります。
※ただし、高い負荷と高速回転が同時に要求される過酷な条件下では、浸炭焼入れや窒化処理などの表面硬化処理を施した合金鋼や、より耐熱性・強度に優れた特殊合金鋼などが不可欠となります。また、適切な潤滑システムの設計も非常に重要になります。
使用環境(温度・湿度・腐食性)
歯車が使われる環境によっては、腐食・温度変化・湿気などが材料の寿命に大きく影響します。
- 高温環境(例:エンジン周辺)→ 耐熱合金鋼、PEEKなどの耐熱樹脂
- 高湿度・水中使用(例:ポンプ、屋外)→ ステンレス鋼(SUS304)、樹脂製ギア(吸水性要注意)
- 腐食性のある環境(例:化学プラント)→ SUS系ステンレス、PPS・PEEKなど耐薬品樹脂
- 低温環境(例:冷蔵設備)→ ナイロンは硬化しやすいため、POMの方が安定性あり
環境条件に適さない材料を使用すると、急激な摩耗、錆び、脆性破壊の原因になります。
潤滑の有無・メンテナンス性
潤滑ができるかどうか(または潤滑を避けたいか)も、材料選定の大きなポイントです。
- 潤滑可能な機構 → 適切な潤滑剤(グリース、オイルなど)を使用することで、金属歯車でも摩耗や騒音を効果的に低減し、長寿命化を図ることが可能。
- 潤滑困難な箇所(密閉空間、給油不可など)→ 自己潤滑性に優れたポリアセタール(POM)やポリアミド(PA)などの樹脂歯車が有効。
- 長期的に無潤滑で使いたい → フッ素樹脂(PTFE)を添加したポリアセタール(POM)や、オイルを含浸させたポリアミド(PA)など、耐摩耗性や自己潤滑性をさらに向上させた特殊グレードの樹脂材料を検討することが有効。
潤滑が不要な設計は、定期的なメンテナンス(給油作業)の工数を削減できるだけでなく、潤滑剤のコストや、潤滑剤による周辺環境への影響を低減できるというメリットもあります。
コスト(材料費+加工費)
設計上、どうしても気になるのがコストの問題です。材料費だけでなく、加工の難易度・熱処理の有無・生産量によってもコストは大きく変動します。
- 単品製作/少量生産 → 比較的安価で汎用的な炭素鋼(S45Cなど)や、切削加工や成形が容易なポリアセタール(POM)などが、初期費用を抑えやすく、納期も比較的短縮できるため有利な選択肢となる。
- 量産品 → 射出成形による高い生産性と寸法安定性を活かせる樹脂製ギアや、鋳造による複雑形状の大量生産に適した鋳鉄ギアなどが、個あたりのコストを低く抑えるために有効な手段となる。
- 高精度仕上げが必要 → 焼入れなどの熱処理後に精密な歯面研削(歯研)が可能な合金鋼や、歪みが少なく研削性に優れた特殊鋼などを選定する必要がある。
樹脂製品は、射出成形を行うために高価な金型の製作が必要となるため、初期投資は高くなりますが、一度金型が完成すれば、サイクルタイムが短く大量生産が可能となり、結果として一個あたりの部品コストを大幅に低減できます。
加工性(製造方法との適合)
材料によって適した加工方法が異なり、求める精度・生産スピード・機械設備との適合が重要です。
- 複雑形状/軽量化 → 射出成形による高い成形自由度と軽量性を活かせる樹脂材料が有利。
- 高精度な噛み合わせが必要 → 熱処理によって硬度を高めた金属材料(合金鋼など)を、精密な歯切り加工後に歯面研削(歯研)によって仕上げる方法が一般的。
- 形状の自由度が高い方がよい → 鋳造性に優れ、複雑な形状を比較的容易かつ安価に製造できる鋳鉄が適している。
また、材料を選定する際には、必要な強度や耐摩耗性を得るための熱処理(焼入れ、焼戻し、浸炭焼入れなど)、あるいは耐食性や表面硬度を高めるための表面処理(窒化処理、メッキ処理など)が適用可能であるかどうかも、重要な加工性の検討項目となります。
まとめ:材料選定は「現場の条件」をよく見ることが重要
材料の選定は、単にカタログスペックで決められるものではなく、実際に歯車が使用される状況に即して考えることが不可欠です。
「どういう場所で」「どれくらいの力がかかり」「どういうメンテナンス体制なのか」——こういった条件を整理することで、最適な材料が見えてきます。
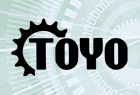