歯車は、私たちの身の回りにある多くの機械に組み込まれており、自動車、時計、産業機械、ロボットなど、あらゆる分野で活躍しています。その中で「歯形(はがた)」は、歯車の機能性や性能を左右する非常に重要な要素です。歯形の違いは、動力の伝わり方や滑らかさ、摩耗のしやすさ、騒音、さらには歯車の寿命にまで影響を及ぼします。
歯車の歯形にはいくつか種類がありますが、特に代表的でよく使われているのが「インボリュート歯形」と「サイクロイド歯形」の2つです。どちらもそれぞれに明確な特徴と用途があり、設計や使用される機械の条件によって適切な選択が求められます。
この記事では、まずインボリュート歯形とサイクロイド歯形の基本的な違いをわかりやすく解説したうえで、それぞれの歯形が持つ特徴、利点・欠点、そして実際にどのような用途で使われているのかをご紹介します。歯車設計や機械工学に携わる方はもちろん、工学初心者や製品開発の現場で歯車選定に関わる方にも役立つ内容となっています。
「なぜこの歯形が選ばれるのか?」「歯車の性能にどのような影響があるのか?」といった疑問を解決しながら、最適な歯形選びのヒントをつかんでいきましょう。
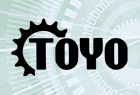
歯形の種類と特徴 – 代表的な2つの歯形
現代の機械設計において、歯車の形状は単なる見た目の違いではありません。特に「歯形(はがた)」と呼ばれる歯の輪郭形状は、回転運動の伝達効率、トルクの安定性、寿命、さらには騒音や振動の抑制といった性能に深く関わってきます。
なかでも、長い歴史と豊富な実績を持つ「インボリュート歯形」と「サイクロイド歯形」は、それぞれ独自の理論に基づき発展してきた代表的な歯形です。一見似たように見える両者ですが、その成り立ちやかみ合い方、力の伝達方法には明確な違いがあり、用途に応じた適切な選定が欠かせません。
本記事では、これら二つの歯形に焦点を当て、それぞれの形状的な特徴や設計理論、どのような場面でその特性が活かされるのかを詳しく見ていきます。機械要素の設計や選定に関わる方にとって、歯形の理解は効率的かつ信頼性の高い機械を作るための基礎知識ともいえるでしょう。
インボリュート歯形
インボリュート曲線とは
「インボリュート(involute)」とは、日本語では「展開線」とも呼ばれ、円周に巻きつけた糸を引っ張りながら解いていくとき、糸の端が描く軌跡を指します。この軌跡をもとに歯形を構成するのがインボリュート歯形です。
この曲線の最大の特徴は、接触角(=圧力角)がかみ合い中に常に一定であること。これは動力伝達を滑らかかつ安定的にする上で極めて重要な性質であり、多くの産業機械にインボリュート歯形が採用されている理由のひとつです。
インボリュート歯形の形状と特徴
インボリュート歯形は、基礎円(base circle)という理論上の円を起点として、インボリュート曲線に沿って形成されます。歯の輪郭はこの曲線で構成されるため、歯同士がかみ合うとき、常に一定の圧力角(例えば20°)で接触が行われ、効率的な動力伝達が可能となります。
主な特徴
- 圧力角が一定:かみ合い中の力の向きが一定になり、振動が少なく安定した回転が得られる。
- 歯面の滑りが比較的少ない:一部では滑りは生じますが、運転効率は高め。
- 歯の高さやピッチ、モジュールなどの標準化が進んでいる:設計・製造が容易で、互換性も高い。
具体的な使用例
- 自動車のトランスミッション
- ポンプやコンプレッサー
- ロボットアクチュエーター
- モーター駆動系のギアユニット
とくに大量生産が必要な分野や、厳しい公差の中で組み立てられる部品においては、インボリュート歯形の再現性と組み立て誤差に対する寛容性が大きな利点になります。
インボリュート歯形の利点・欠点
利点
- かみ合い時の接触が滑らか
常に一定の圧力角でかみ合うため、トルクの伝達が均一で、衝撃が少ない。 - 製造・設計の標準化が進んでいる
モジュールや圧力角など、国際的な規格が整っており、互換性のある部品の設計がしやすい。 - 組み立て誤差に強い
軸間距離が多少ずれても、動力伝達に支障をきたしにくい(「共役作用」が保たれる)。 - 製造コストが比較的安価
工具や加工技術が普及しており、歯切り加工や研削の工程も確立している。
欠点
- 歯面同士の滑りによる摩耗
かみ合いの始まりと終わりには滑りが生じやすく、高精度かつ長寿命を要求される場面では注意が必要。 - 歯先が薄くなりやすく、欠けやすい
極端なトルクがかかると、歯の先端が破損するリスクがある。 - 低速で高トルクを伝える用途では効率が下がる
特に精密制御が必要な機器には不向きな場合もある。
補足:インボリュート歯形の進化と将来性
インボリュート歯形は19世紀に本格的に機械設計へ取り入れられて以来、産業機械の中心的存在であり続けています。現在では、複雑なCAD/CAM技術や5軸加工機の進化により、より高精度な歯形加工も可能となっています。また、歯面処理や新素材の応用により、摩耗耐性や寿命の延伸も実現されつつあります。
サイクロイド歯形
サイクロイド曲線とは (エピサイクロイド、ハイポサイクロイド)
サイクロイド曲線は、円の周上にある点が、他の円の外周または内周を転がるときに描く軌跡です。外周を転がる場合の軌跡は「エピサイクロイド」、内周を転がる場合は「ハイポサイクロイド」と呼ばれます。
歯車のサイクロイド歯形では、歯先(外側の輪郭)をエピサイクロイド、歯底(内側の輪郭)をハイポサイクロイドで形成するのが一般的です。この曲線によって、かみ合いの際の滑りを限りなく少なくし、摩耗の低減とスムーズな回転運動を実現しています。
サイクロイド歯形の形状と特徴 (創成円など)
サイクロイド歯形の形成には「創成円(rolling circle)」と呼ばれる円が用いられます。この創成円を転がし、その外周・内周の軌跡によって歯の形状が生成されます。
インボリュート歯形と異なり、サイクロイド歯形では圧力角が一定ではなく、かみ合いの位置によって変化するという特徴があります。しかしその代わりに、かみ合いの開始・終了時における滑りがほとんどなく、歯面の摩耗が極めて少ないという利点があります。
主な特徴
- 滑りが少なく摩耗しにくい:特に精密機構では大きなメリット。
- 歯面の接触が点ではなく面に近いため、接触応力が分散される。
- 圧力角が変化するため、設計・解析はやや複雑。
- 自動補正が効きにくく、軸間距離の誤差に弱い。
サイクロイド歯形の利点・欠点
利点
- かみ合いの滑りがほとんどない
エピサイクロイド・ハイポサイクロイドの組み合わせにより、回転初期から終点まで摩擦が非常に少ない。 - 摩耗が少なく寿命が長い
歯面の負担が小さいため、耐久性が求められる機構に適している。 - 静音性に優れる
振動や衝撃が抑えられる構造のため、回転音が非常に静か。 - コンパクトで高トルク伝達が可能
減速比を大きく取りやすく、省スペース設計に向いている。
欠点
- 軸間誤差に弱い
インボリュート歯形のような「共役作用」がないため、歯車の取り付け精度が厳密に要求される。 - 製造が難しい
複雑な曲線を正確に加工する必要があり、一般的な歯切り工具では対応しにくい。 - 汎用性が低い
設計と製造に専用技術が必要なため、量産品や標準部品にはあまり用いられない。
歯車設計における歯形の重要性 – 用途との関連性
歯車設計において、歯形の選定は単なる形状の選択にとどまりません。使用環境、要求される性能、コスト、加工精度、メンテナンス性など、さまざまな条件を考慮したうえで、最適な歯形を選ぶ必要があります。ここでは、インボリュート歯形とサイクロイド歯形がそれぞれどのような用途で活かされているか、その理由を具体的に見ていきましょう。
インボリュート歯形が適している用途
(例:一般的な動力伝達、高トルク伝達)
インボリュート歯形は、現在もっとも広く使われている歯形であり、その安定性・加工のしやすさ・軸間誤差に対する寛容さなどが大きな強みです。以下のような場面に最適です。
- 自動車のトランスミッション
→ 高速回転・高トルク伝達が求められ、かつ量産性が必要。インボリュート歯形なら効率よく安価に生産可能。 - 産業用減速機・ポンプ類
→ 駆動力の伝達と耐久性が重要であり、標準化されたインボリュート歯形がメンテナンスにも有利。 - ロボットアームの駆動部
→ 精密なトルク制御と部品交換のしやすさが求められ、互換性の高い歯形が重宝される。 - 汎用モーターや機械装置全般
→ 部品数が多く組み立てにバラつきが出やすいが、インボリュート歯形は軸間誤差に強いため信頼性が高い。
このように、インボリュート歯形は「多様な設計要求を無理なく満たす」という点で非常に優れており、工業製品全般において実質的な“標準”となっています。
サイクロイド歯形が適している用途
(例:精密機器、低速高トルク伝達)
一方、サイクロイド歯形は、加工や設計の難しさがあるものの、摩耗の少なさ・高トルク伝達・静音性といった面で特に強みを発揮します。
- 機械式時計
→ 極めて微細な力を正確に伝える必要があり、摩耗の少ないサイクロイド歯形が理想的。 - ハーモニックドライブや遊星減速機
→ 小型軽量でありながら、大きなトルクを滑らかに伝える必要がある。滑りのないかみ合いが重要。 - 精密医療機器や光学機器の駆動系
→ 振動や騒音の発生を最小限に抑えつつ、高精度で制御される回転が必要とされる。 - 一部の工作機械や印刷機構
→ 駆動系の滑らかさが製品品質に直結する分野では、サイクロイド歯形の特性が活かされる。
サイクロイド歯形は「限られた条件下で最大限の性能を発揮する」歯形です。設計の自由度は小さいものの、特化型の用途においては替えの効かない選択肢となります。
歯形設計における寸法と公差
(歯形精度が性能に与える影響など)
どちらの歯形を選ぶにしても、正確な寸法設計と高精度な加工は不可欠です。歯形のわずかな誤差が、以下のような不具合を招く可能性があります。
- かみ合いの異音・振動
- 効率の低下・摩耗の増加
- トルク伝達の不安定化
- 長期使用時のガタつき・バックラッシュの増大
特にサイクロイド歯形は軸間距離や歯形精度の影響を強く受けるため、精密な設計と加工が要求されます。インボリュート歯形は比較的公差に寛容とはいえ、高回転・高負荷の場面では同様の精度が求められます。
まとめ – 特性を理解し、最適な歯形選択へ
歯車の性能や寿命は、歯形の選定によって大きく左右されます。インボリュート歯形とサイクロイド歯形、それぞれに明確な特徴と用途があり、設計要件に応じた適切な選択が不可欠です。
最終的に重要なのは、「どの歯形が一番優れているか」ではなく、「どの歯形が用途に合っているか」です。歯形の特性を正しく理解し、使用環境や要求性能に応じて最適な選択を行うことが、信頼性の高い機械設計の第一歩と言えるでしょう。